Kunst des Glattwalzens
Die Oberflächenbehandlung im Kaltverfahren dient vor allem zur:
• Optimierung der Oberflächenendbearbeitung
• Erhöhung der Festigkeit
• Verbesserung der Maßkalibrierung
Der wichtigste Ansatz besteht darin, eine plastische Umformung des Werkstücks hervorzurufen, indem es einer relativ geringen Druckspannung ausgesetzt wird, um eine höhere Oberflächenfestigkeit zu erreichen. Zu diesen Verfahren zählen: Glattwalzen, Schälen, Feinwalzen.
Wenn eine relativ geringe Kraft mit einer feinpolierten Walze, die Drehbewegungen ausführt, eingesetzt wird, wird diese Walze geradlinig über das Metallwerkstück geführt. Dieser Vorgang wird Glattwalzen genannt.
Die Herstellung von Glattwalzwerkzeugen ROBUTO® – begann 1985 in der Türkei. Am Anfang waren diese Werkzeuge vor allem für die Innen- und Außenbearbeitung gedacht. Derzeit werden unterschiedliche Verfahren entwickelt und untersucht, die sich nach dem Stand der Technik richten. Es werden auch Sonderentwürfe für Industrieanwendungen erstellt.
GLATTWALZEN
Die Aufgabe dieses Verfahrens ist es, die von der Rolle ausgeübte Kraft auf die Oberfläche in einer bestimmten Bahn zu übertragen.
Bei der Drehbewegung der möglichst geringen Kontaktfläche muss an dieser Stelle eine Druckspannung mit einer möglichst geringen Frequenz erzeugt werden, die wenig Energie und Kraft erfordert.
Das Glattwalzen von Metalloberflächen ist nur mit dem Einsatz von speziell entworfenen Rollen und Stielen sowie deren Kombinationen möglich.
Auf der Zeichnung Nr. 1 ist das Glattwalzverfahren mit einer rundförmigen Rolle schematisch dargestellt (A) erste Kontaktstelle mit dem Werkstück. (B) Überschreitung der Werkstoffstreckgrenze und die daraus resultierende plastische Verformung. (D) Drucktiefe. Wenn das Werkstück die maximale Verformung im Bereich (C) überschreitet, fängt es an, sich plastisch zurückzuformen. (E) Glattgewalzte Oberfläche, glatte Oberfläche und die nach der Verformung bestehende Spannung.
Die im Werkstück beim Pressvorgang entstehende Spannung verringert sich in Richtung Mitte. Die Eigenspannung beträgt unter der Oberfläche ca. 1 mm und trägt somit zur Erhöhung der Oberflächenfestigkeit bei.
Die Werkzeuge ROBUTO® bestehen aus einem Stiel mit Rolle, die in einem Käfig befestigt sind. Diese Ausführung gewährleistet eine äußerst maßgenaue Werkstückbearbeitung.
ERGEBNISSE DES GLATTWALZVERFAHRENS
• Rauheit von 0,05 bis 0,10 μm. (Ra) – (ISO N2, N3)
• Toleranz 0,01 mm oder noch präziser
• Erhöhung der Oberflächenhärte von 30% bis 70%
• Erhöhung der Zug- und Ermüdungsfestigkeit über 300%
• Eliminierung von korrosions- und rissbildenden Spannungsfaktoren
• Erhöhung der Korrosionsfestigkeit
• Eliminierung von korrosions- und rissbildenden Spannungsfaktoren
• Reduzierung der Reibung um mehr als 35%
• Reduzierung des Schallpegels
Einsatzgebiete der Glattwalzwerkzeuge ROBUTO
• Symmetrische / halbsymmetrische Elemente
• Innenbearbeitung, zylindrisch
• Außenbearbeitung, zylindrisch
• Innenbearbeitung, mit Verengung
• Außenbearbeitung, kegelförmig
• Runde und ebene Oberflächen
• Sie können in allen Maschinen eingesetzt werden (Bohrmaschinen, Drehmaschinen, Bearbeitungszentren oder sonstige Drehspindeln).
• Max. Härte der Werkstücke 40 HRC
Vorteile der Glattwalzwerkzeuge im Vergleich mit herkömmlichen Bearbeitungsverfahren
• Glattwalzverfahren sind günstiger als Schleifen, Honen und Läppen.
• Die im Glattwalzverfahren erzeugte Rauheit der Oberfläche ist geringer bzw. vergleichbar mit der Oberfläche bei zerspanenden Verfahren. Auch die erzielten Werte sind vergleichbar; eine mit Hilfe von Rollen bearbeitete Oberfläche ist glatter als eine geschliffene Oberfläche, weil bei Prozessen der Zerspanungstechnik scharfe Rauheitsspitzen an den Kontaktstellen entstehen.
• Bei Einzelteilen mit einem Durchmesser von 30 mm und einer Länge von 100 mm dauert der Glattwalzvorgang etwa 10 bis 15 Sekunden
• Keine kostspieligen Investitionen erforderlich
• Mechanische Vorteile (Korrosionsbeständigkeit, Erhöhung der Oberflächenhärte).
• Kürzere Prozesszeiten und geringe Kosten. Ohne zusätzliche Instandhaltungskosten kann man von 10.000 bis 300.000 Einzelteile bearbeiten
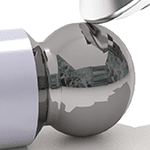
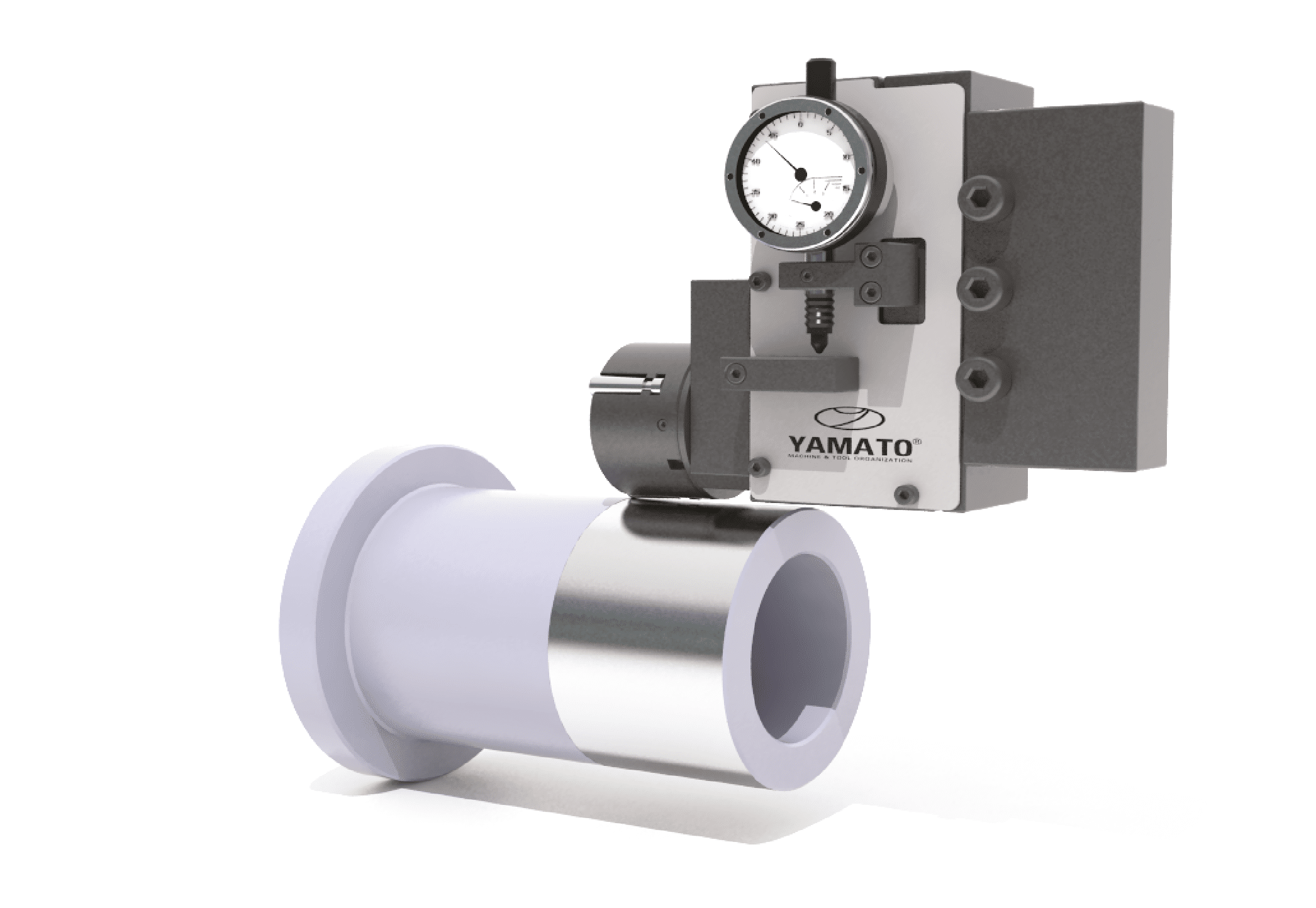
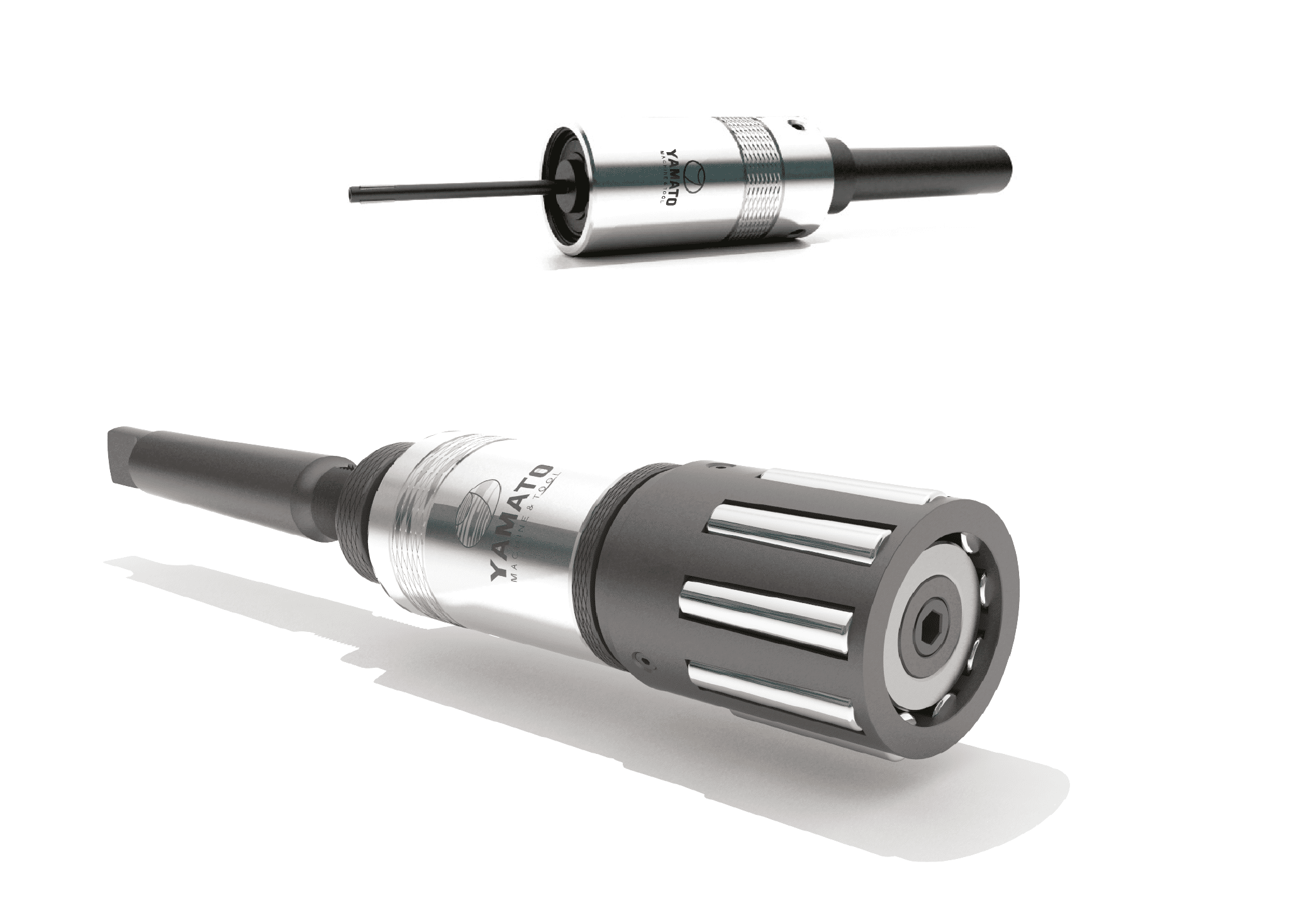
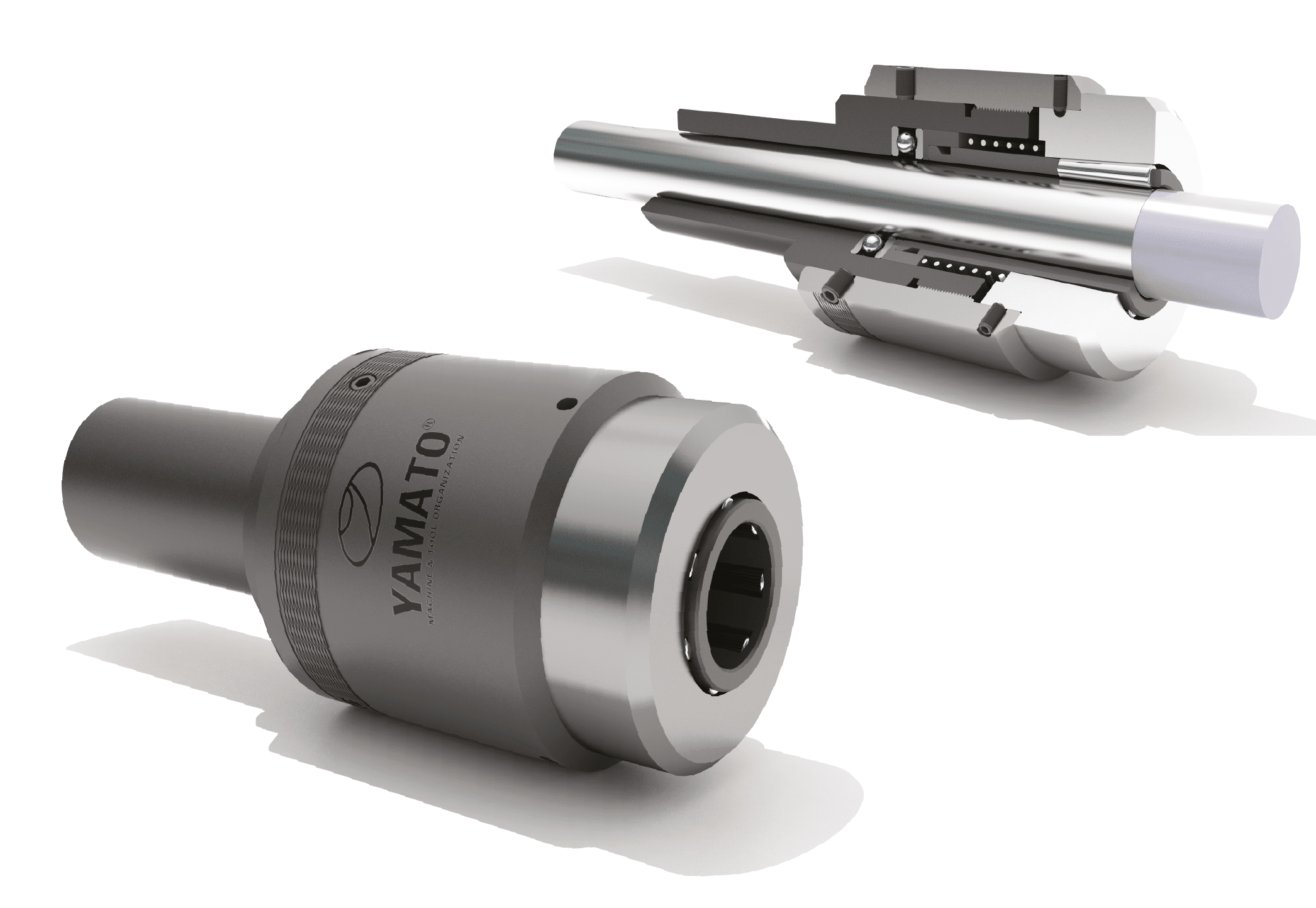